彩色紙箱子一般全是4色之上的版面開展套印,且面巾紙的橫著非常容易因自然環(huán)境的溫度濕度轉(zhuǎn)變而出現(xiàn)形變,導(dǎo)致套印禁止常見故障的造成。控制好印刷生產(chǎn)車間的溫度濕度,變成提升彩色紙箱子商品套印精密度的重要一環(huán)。
Color paper boxes are usually overprinted on 4 colors, and the cross section of tissue paper is easy to deform due to the change of temperature and humidity in the natural environment, which leads to the common failure of overprint prohibition. Controlling the temperature and humidity of printing workshop becomes an important part of improving the overprint precision of color paper box products.
因此,無論是柔印加工工藝、平印或凹印生產(chǎn)線,生產(chǎn)制造當(dāng)場的溫度濕度都務(wù)必維持相對性的平穩(wěn)和均衡,印刷全過程中不能出現(xiàn)顯著的高矮差距狀況,以防造成套印禁止的弊端。印刷加工工藝實(shí)踐活動說明,印刷生產(chǎn)線的溫度一般控制在22℃上下,環(huán)境濕度應(yīng)維持在60%上下,紙型、硬紙板不易出現(xiàn)形變狀況,那樣對不錯確保商品的精確套印是較為合理的。
Therefore, no matter it is flexo printing process, lithography or gravure production line, the temperature and humidity on the production site must be kept relatively stable and balanced, and there should be no significant height gap in the whole printing process, in order to prevent the malpractice of overprint prohibition. The practice of printing process shows that the temperature of the printing production line is generally controlled at 22 ℃, and the ambient humidity should be maintained at 60%. The paper shape and cardboard are not easy to deform, which is good for ensuring the accurate overprint of commodities.
2、裝版生產(chǎn)工藝控制。
2. Plate loading production process control.
選用膠印機(jī)對紙箱子面巾紙開展預(yù)印的生產(chǎn)工藝流程,裝版實(shí)際操作技術(shù)性的控制非常關(guān)鍵。因?yàn)镻S版較薄,其光感應(yīng)層和版基的累計薄厚約為0.2mm,而且鋁合金板的版基,原材料具備較脆的特點(diǎn),在裝版全過程時要留意慎重實(shí)際操作,上版時要留意防止版面被設(shè)備上的構(gòu)件刮傷;
Using offset press to carry out preprinting process for box tissue paper, the technical control of actual plate loading is very important. Because the PS plate is thin, the cumulative thickness of its light sensing layer and plate base is about 0.2mm. Moreover, the raw materials of the plate base of aluminum alloy plate have the characteristics of brittleness. In the whole process of plate installation, pay attention to the practical operation, and pay attention to prevent the plate from being scratched by the components on the equipment;
校版拉版時要留意把握適當(dāng)用勁,避免用力過猛而使印刷版出現(xiàn)拉申形變,導(dǎo)致商品套印禁止和耐印率降低。柔版裝版要留意盡可能一次性指向粘版部位,防止不斷拆版使印刷版形變和危害粘版的色牢度。
When proofreading and printing, we should pay attention to the proper use of force to avoid drawing deformation of the printing plate due to excessive force, resulting in the prohibition of overprinting and the reduction of printing endurance. Flexographic mounting should pay attention to the one-time point to the sticky part as far as possible, to prevent the continuous plate breaking deformation and damage the color fastness of the plate.
當(dāng)平均氣溫非常高時,應(yīng)考慮到選用高品質(zhì)的泡沫雙面膠,避免印刷全過程中印刷版出現(xiàn)走位常見故障。高品質(zhì)的泡沫雙面膠布應(yīng)該是黏度強(qiáng),平面度好,薄厚勻稱,耐熱性能優(yōu)良,能保證 在高、超低溫工作自然環(huán)境下維持黏度的可靠性,拆版時版材和版滾桶沒留膠痕。
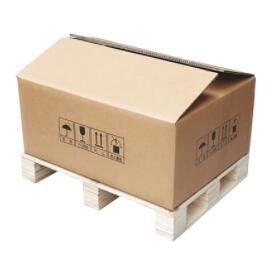
When the average temperature is very high, we should consider the choice of high quality foam double-sided adhesive to avoid common faults in printing process. High quality foam double-sided adhesive tape should be strong viscosity, good flatness, thin and well proportioned, excellent heat resistance. It can ensure the reliability of maintaining viscosity in high and ultra-low temperature working environment.
3、膠版印刷墨筆畫均衡的控制。墨筆畫均衡的控制是膠版印刷加工工藝關(guān)緊要的一個技術(shù)性階段,在印刷面巾紙時經(jīng)常由于墨筆畫均衡控制不及時,危害淡墨品質(zhì)的狀況不缺出現(xiàn),因而在印刷全過程中,要以盡可能小的潤版液需求量,在維持墨筆畫均衡的標(biāo)準(zhǔn)下開展理想化的印刷,切勿選用“墨洪水也大”的均衡法開展印刷。
3. Offset printing ink painting balance control. The control of ink brush balance is a crucial technical stage in offset printing process. When printing facial tissue paper, due to the untimely control of ink balance, there is no lack of damage to the quality of light ink. Therefore, in the whole process of printing, it is necessary to carry out ideal printing with the minimum amount of fountain solution as possible under the standard of maintaining ink and brush balance“ Ink flood also big "balanced method to carry out printing.
墨筆畫均衡控制的關(guān)鍵所在,規(guī)定油墨保持穩(wěn)定的潔凈度和有效的流通性,要盡可能無需或者少用催干劑,避免油墨初期干躁出現(xiàn)的起膜狀況;印刷生產(chǎn)車間要注意防塵、防粉維護(hù);要盡量減少新老油墨互用;潤版液PH值控制要適度,水體要維持純粹;膠棍和水輥務(wù)必保持穩(wěn)定的精密度和適度的強(qiáng)度;印刷速率要維持適度和穩(wěn)定,這種全是完成墨筆畫均衡的技術(shù)性要點(diǎn)和合理確保標(biāo)準(zhǔn)。
The key to the balance control of ink and brush painting is to stipulate that the ink should keep stable cleanliness and effective circulation, and the drying agent should be avoided as much as possible, so as to avoid the film forming condition of the ink in the early stage of dryness; the printing workshop should pay attention to the dust and powder proof maintenance; the new and old inks should be used as much as possible; the pH value of fountain solution should be controlled appropriately, and the water body should be kept pure; rubber stick and water roller should be kept It is necessary to maintain stable precision and moderate strength, and to maintain moderate and stable printing speed, which are the technical points and reasonable assurance standards for completing the balance of ink and brush painting.
4、膠版印刷印刷色序分配的控制。
4. Control of color sequence distribution in offset printing.
彩色紙箱定做的印刷一般全是選用多色印刷機(jī)一次進(jìn)行印刷的,印刷時油墨是在一瞬間進(jìn)行“濕壓濕”的疊印和套印的,各色各樣中間疊壓的時間非常短,因此,印刷色序應(yīng)依據(jù)版面構(gòu)造、油墨特點(diǎn)和紙型特性等眾多要素有效明確。
The multi-color printing machine is generally used for one-time printing of color cartons. When printing, the ink is used to overprint and overprint in a flash, and the time of intermediate lamination of various colors is very short. Therefore, the color sequence of printing should be effectively defined according to the layout structure, ink characteristics and paper type characteristics.
一般來說,印刷色序的分配應(yīng)依據(jù)具體情況酌情考慮把握,如將印刷總面積和墨量小的先印,版面和墨量大的后??;清晰度差的油墨先印,清晰度好的油墨后?。火ざ却蟮挠湍扔?,黏度小的油墨后?。黄陕挠湍扔?,干躁速度更快的油墨后印。
Generally speaking, the distribution of printing color sequence should be considered according to the specific situation, such as printing the printing with small total printing area and ink quantity first, printing after printing with large layout and ink volume; printing ink with poor clarity first, printing with ink with good clarity; printing with high viscosity first, printing with oil ink with low viscosity; printing with slow drying ink first, printing with ink with faster drying speed.